The industrial landscape across the globe has been transformed due to metal 3D printing due to its advantages of high customizability, low production cost, and meeting tight deadlines. It is no surprise that San Diego being at the center of various technologies has been quick to adopt this form of advanced manufacturing to suit industries such as aerospace, automotive, healthcare, and energy, among others.
This guide talks about metal 3D printing, some of the advantages, and the primary applications in the state of San Diego. Further, this guide also details how businesses can tap into the full potential of metal 3D printing for industrial applications.
What is Metal 3D Printing
By definition metal 3D printing or metal additive manufacturing is a process of creating complex metal parts from a cad file through a layer by layer process. Metal powders such as stainless steel, titanium, aluminum, cobalt and chromium are used in this technique and are joined together using lasers or electron beams.
Common Metal 3D Printing Technologies:
Direct Metal Laser Sintering (DMLS): Suitable for use cases looking to achieve intricate details of a part whilst maintaining high strength.
Selective Laser Melting (SLM): Is known to have a good energy density and durability.
Electron Beam Melting (EBM): This technology thrives in high temperature applications.
Binder Jetting: Also produces parts, but for the thinner sections it requires more energy to melt the powders.
Why Metal 3D Printing is Important for Industry Applications
Design Freedom
The main limitation of traditional means of manufacturing approaches are the design constraints but with the use of metal 3D printers, complicated shapes and lightweight structures can be achieved while still being extremely strong.
Cost and Time Efficiency
The amount of materials used is less, molds as well as toolings are not required in additive manufacturing which also decreases the costs. Additive manufacturing processes work best for prototype making as well as small production runs as they cut the time taken to make the prototypes as well as the cost involved.
Enhanced Customization
Custom made parts can be produced by Industries by being able to meet actual requirements which improves the level of performance along with product effectiveness.
Sustainability
Because there is little waste and energy consumption is reduced, metal 3D printing is a more sustainable option than traditional manufacturing.
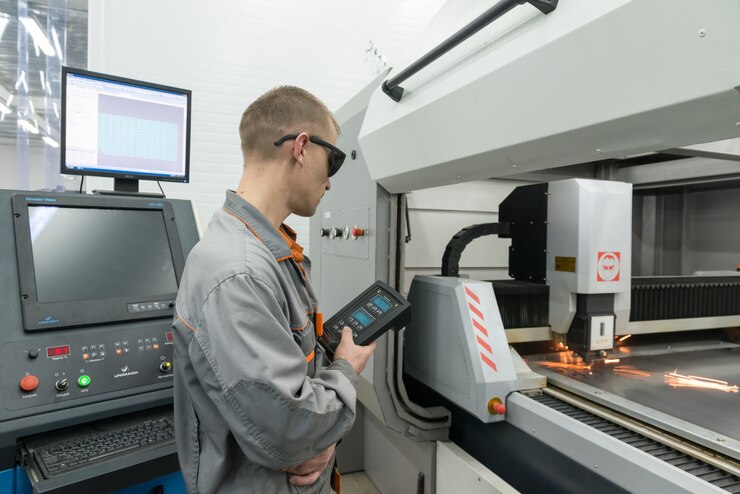
Applications of Metal 3D Printing in San Diego
Aerospace and Defense
San Diego aerospace industry focuses mainly on metal 3D printing to manufacture lightweight parts which include components such as blades for turbines, engine parts and structural components. This allows for the parts to be strong and precise enough for the aerospace industry as well as reducing the time taken to make them.
Automotive
Metal 3D printing is used by the Automotive manufacturers to manufacture some engine parts, iniature and new versions of prototype designs which allows for new designs to be made in a short period of time.
Healthcare
Medical devices designed for use in San Diego use titanium in metal 3D printing to manufacture implants, prosthetics as well as surgical instruments which allow for the implants to integrate well with the body and be durable.
Renewable Energy
Marine applications such as constructions of wind turbines and heat exchangers as well as sea urchin based custom fixtures are manufactured through metal 3D printing.
Tooling and Die Manufacturing
San Diego large size means that there are many sectors and industries that possess distinct aspirations. This is where metal 3D printing shines. By allowing for the easy creation of molds, tools and dies 3D printing further aids San Diego in its growth.
How to Choose a Metal 3D Printing Service in San Diego
Evaluate Material Options
Start by verifying whether or not the 3d printing provider has what you are looking for, suppliers who have titanium kits may have aerospace while stainless steel would do those in automotive manufacturing.
Check Technological Expertise
Some services are already-equipped with advanced technologies like DMLS or SLM to ensure high results in terms of precision and quality.
Assess Industry Experience
It is probable that businesses that have successfully executed projects in your sector understand its requirements.
Consider Turnaround Times
For some projects, speedy delivery may be crucial in order to maintain the timeline. As a result, go for a business that is known for contact ensuring quick delivery of orders.
Verify Certifications
Before getting any manufacturing undertaken it is recommended to check the manufacturing company whether they have ISO or other authorized certifications related only to the industry.
Future Trends in Metal 3D Printing
Advanced Alloys and Materials
There is significant space for development when it comes to alloys and composites for the basic metals that can enhance performance for multiple applications and the research centers in san Diego are expected to be at the forefront.
AI-Driven Design Optimization
Integration of AI artificial intelligence into 3D printing processes virtually eliminates production errors and improves the designs’ efficacy.
Scaled Manufacturing
With the prices still falling the expectation is for metal 3D printing to be applied from the development of models to its mass production.
Hybrid Manufacturing
Increasingly becoming the norm is the use of both additive and subtractive approaches as they provide unmatched accuracy and flexibility.
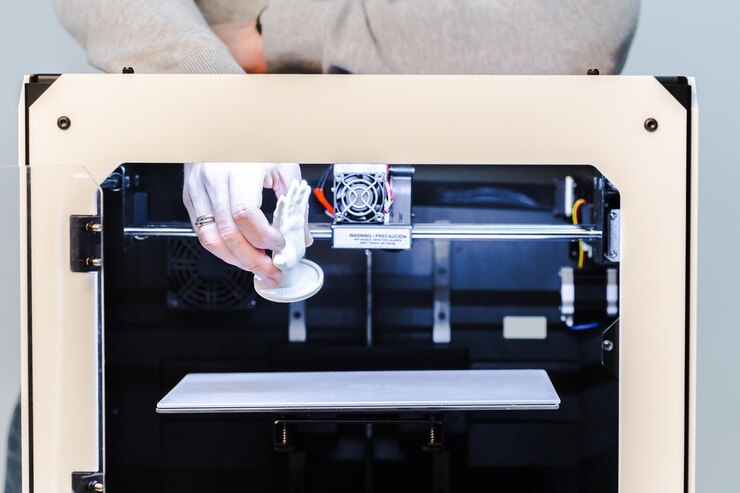
Challenges and How to Overcome Them
High Initial Costs
Solution: Join forces with service providers rather than purchasing in-house apparatus.
Material Limitations
Solution: Research on advancement of materials and seek partnerships with research bodies.
Post-Processing Requirements
Solution: Find providers who can offer full cycle services starting from post-processing.
Skill Gap
Solution: Enhance employee training and development or recruit 3D printing skill-required personnel into the company.
Maximizing the Benefits of Metal 3D Printing
In order to benefit entirely possible when talking of the metal 3D printing technology, businesses operating in San Diego should:
Work with Other Agencies: Utilize the local knowledge and other service providers in the process aimed at removing inefficiencies in the workflow patterns.
Channel More Funds in R&D: More funds should be directed toward seeking new use cases along with more achievable technologies.
Go Green: Adopt practices and materials that are environmentally sustainable.
Use New Software: Tools such as CAD and AI have improved the design and production process.
Conclusion
Metal 3D Printing has marked a turning point for industrial operations in San Diego. It has enabled design complexity, speed, and ease that were, until this moment, inconceivable. It is beginning to transform the way key industries operate, including aerospace as well as healthcare. Once a firm masters the technology, partners with qualified service providers, and anticipates developments, there is a lot that can be achieved.
Start exploring the possibilities of metal 3D printing today and take your industrial applications to the next level.
What industries in San Diego benefit most from metal 3D printing?
These are specifically aerospace, automotive, healthcare, and renewable energy”.
How much does metal 3D printing cost?
The cost of metal 3D printing ranges depending on the type of material, the size of the metal, and the complexity involved. Custom parts made through metal 3D printing ranges from $100 to a few thousand dollars.
What are the main materials used in metal 3D printing?
The materials best known to be associated with metal 3D printing include stainless steel, titanium, aluminum, and cobalt-chromium.
Is mass production achievable through metal 3D printing technology?
Researchers in the two countries say scaling has previously been difficult as conventional 3D printing technology was used primarily to make prototypes.
Is it true that metal 3D printing contributes toward the protection of the environment?
Absolutely correct as it creates minimum waste, uses lesser raw materials, and employs methods of production that saves energy when compared to traditional manufacturing techniques.